Note: no Lockheed Martin
proprietary
data is shown here.
OVERVIEW
The Atlas V is Lockheed's design for the USAF's EELV (Evolved Expendable
Launch Vehicle) program. Boeing is also participating with their Delta
IV, which
will ultimately compete against the Atlas V in the commercial launch market.
(The EELV program has carried both designs into production.) The standard
Atlas V variant has about 860,200 lbs of lifting power (thrust) at sea level
take-off, thanks to it's NPO EnergoMash RD-180 engine (1)
(2) (3)
(4),
while the heavy-lift variant has about 2.5M lbs.
The RD-180 production line will be managed by RD AmRoss LLC, a joint-venture
of NPO EnergoMash and Pratt & Whitney Space Propulsion, set up
after technology safeguard agreements between the U.S. and Russia, to protect
Russian technologies and prevent proliferation, were finalized. NPO Energomash
will receive a licensing fee for each engine produced in the U.S., which as of
this writing is expected to start no earlier than 2005.
The Atlas V family is capable of lifting payloads up to 19,100 lb (8,650 kg) to geosynchronous transfer orbit
(GTO).
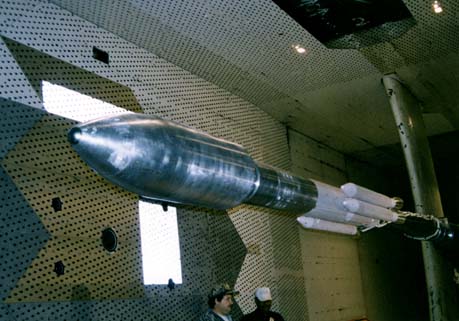
Atlas V "552" configuration in
AEDC wind tunnel.
RECENT STUFF
July 2003: HUGE
EELV INDUSTRIAL ESPIONAGE SCANDAL AT BOEING!! LOCKHEED MARTIN WINS!!
August 2002: Inaugural launch.
Atlas V
launch location at Cape Canaveral Air Station, FL
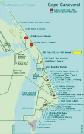
|
what it's launch
complex will look like (Complex 41, Cape Canaveral Air Station, FL)
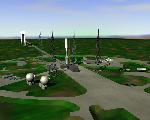
|
First, clear
Complex 41 from Titan IV use...
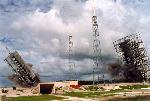
|
...then build
the new Atlas V complex.
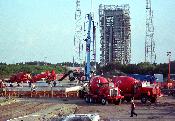
|
Atlas V exploded
views
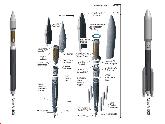
|
Common Core
Booster (CCB) umbilical connector plug & receptacle [recent design]
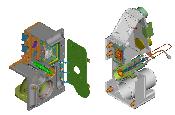
|
mated
pair (the gold receptacle flies away with the rocket) [early design]
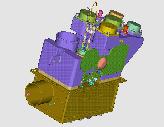
|
Proof
Of Concept CCB prototype (interface region only), plug & receptacle
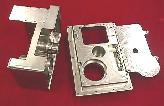
|
Proof Of Concept
CCB prototype, plug
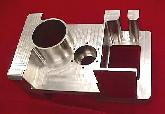
|
Proof Of Concept
CCB prototype, receptacle
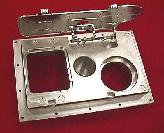
|
Proof
Of Concept CCB prototype, receptacle hinge detail
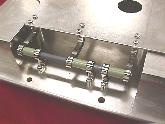
|
Proof Of Concept
CCB prototype, flapper door latch detail (open)
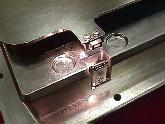
|
Proof Of Concept
CCB prototype, flapper door latch detail (locked)
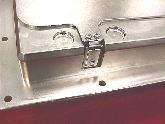
|
Full-Up
Prototype CCB design (plug only shown; housing milled, not cast)
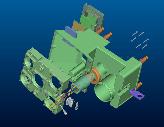
|
Full-Up
Prototype CCB
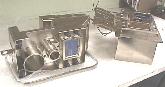
|
Full-Up
Prototype CCB
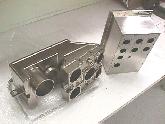
|
Full-Up
Prototype CCB, plug detail
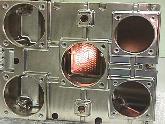
|
Full-Up
Prototype CCB, static pulls test setup (note large solid magnesium
vibration fixture [cube])
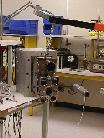
|
Full-Up
Prototype CCB, me doing a mate

|
Full-Up
Prototype CCB, static pulls testing
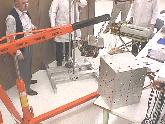
|
Full-Up
Prototype CCB, static pulls testing
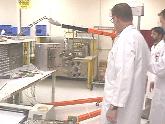
|
Full-Up
Prototype CCB, dynamic (vibration) test setup
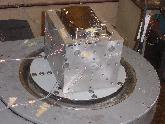
|
Full-Up
Prototype CCB, dynamic (vibration) test to failure

|
Full-Up
Prototype CCB, dynamic (vibration) test to failure

|
CCB
Qualification & Production units' housings in work, plug (cast)
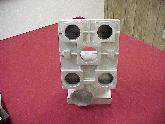
|
CCB
Qualification & Production units' housings in work, plug (post-cast
machining)
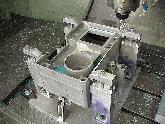
|
MONTHS
LATER: boot the casting vendor and go with massively simplified milled
housings.
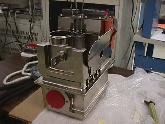
|
Engineering Test
Unit build (~333 signals)
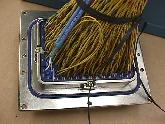
|
Engineering Test
Unit build: bad hair day
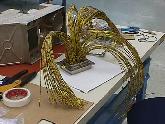
|
Engineering Test
Unit build: disemboweled
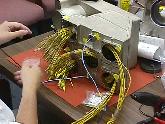
|
Engineering
Test Unit build
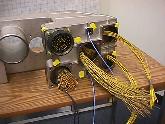
|
Engineering Test
Unit build
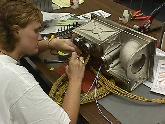
|
Engineering Test
Unit build: 10# of something into a 5# box
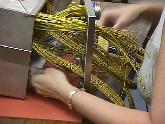
|
Engineering Test
Unit build
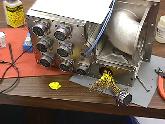
|
Engineering
Test Unit electrical testing: buzzing out lines
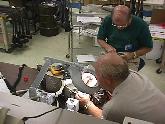
|
Engineering Test
Unit electrical testing: more buzzing out lines
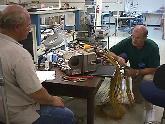
|
the first
CCB flight
vehicle in final assembly in Denver, April 2001
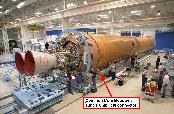
|
CCB rollout ceremony, April 2001. Speaker: Darleen A. Druyun, principal deputy assistant secretary of the Air Force for acquisition and
management (EELV is an Air Force program)
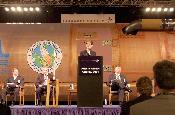
|
CCB
packed up for shipment to the Cape, May 2001
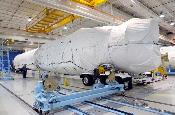
|
Antonov 124
unloads CCB at the Cape, May 2001
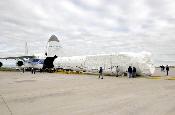
|
our
beefed-up redesign on one of the Qual Units, pre-assembly; from "bad
hair day" to Medusa.
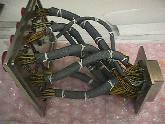
|
CCB EMI Qualification
Testing, February/March 2002
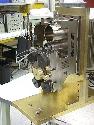
|
CCB Vibration
Qualification Testing, February/March 2002
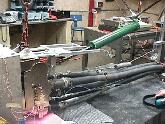
|
RD-180
Throttle-up vibration simulation in 1 axis, up to demate (MPEG4
Video, 5.6 MB)
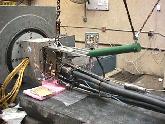
|
March
2002: First roll-out for WDR (Wet Dress Rehearsal), where the bird is tanked and ground ops are ran as would be done for flight (up to launch without lighting the match). Tank RP-1, then tank the Cryos... verify all ground to airborne interfaces, procedures, hardware and software. After WDR comes Sim-flight which carries the testing forward, faking out the Avionics, making the bird think it's
flying.
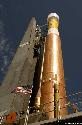
|
Atlas V
heritage
|
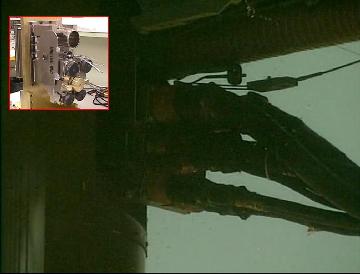
inaugural
launch video, CCB connector in action (AVI
video, 3.0 MB) |
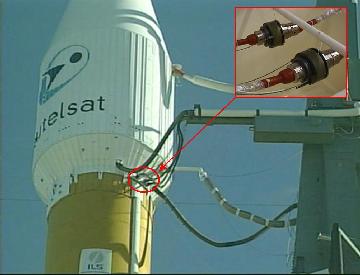
REF: inaugural
launch video, Centaur connector in action -- plus rocket fly-by! (AVI
video, 3.3 MB)
The Centaur
connector was developed at the same time as the CCB connector. There are
3-5 of them per vehicle. |
Atlas V promo
poster
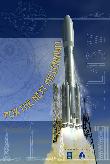
|
Atlas V Payload
Planner's Guide
(1.4 MB, Adobe
Acrobat PDF format)
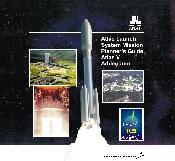
|
and for
reference, just so you can see how big the Atlas V is fully assembled...
Lockheed
Martin Titan IV |